Understanding the Volumetric Concrete Plant: Innovating Construction Practices
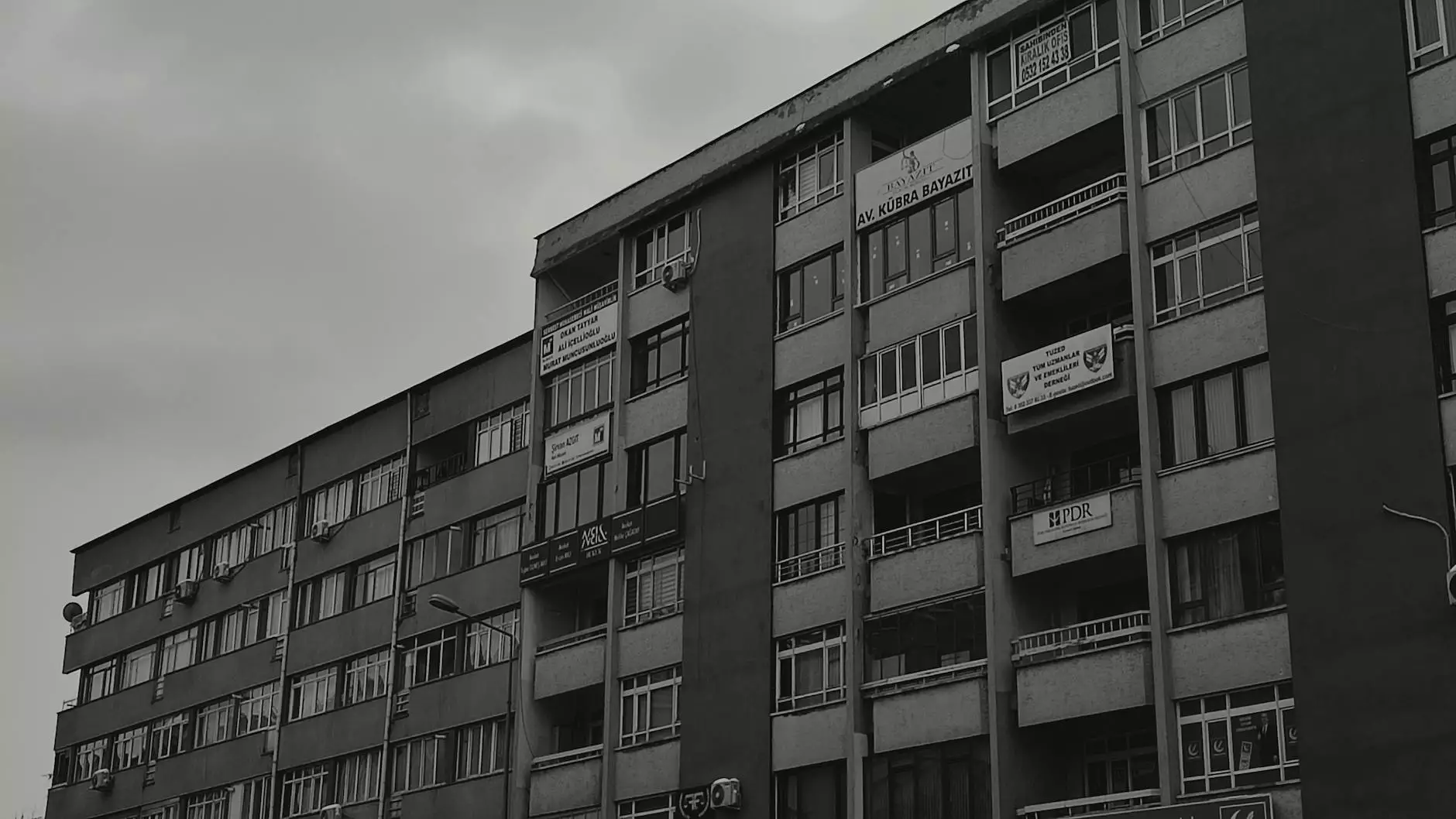
The construction industry is constantly evolving, with new methodologies and technologies emerging to enhance productivity and efficiency. One such game-changer is the volumetric concrete plant, which has revolutionized how concrete is mixed and delivered on-site. In this article, we will explore the ins and outs of volumetric concrete plants, their benefits, and how they are transforming construction practices today.
What is a Volumetric Concrete Plant?
A volumetric concrete plant is a specialized mobile concrete mixer that provides the ability to produce concrete on demand. This state-of-the-art equipment allows construction firms to mix raw ingredients—cement, sand, gravel, and water—in precise volumes, ensuring the production of high-quality concrete tailored to specific construction needs.
Unlike traditional batch mixing plants, where concrete is mixed in large batches and transported to the site, volumetric plants mix concrete in real-time, significantly reducing waste and improving overall project efficiency.
How Does a Volumetric Concrete Plant Work?
The working mechanism of a volumetric concrete plant is fairly straightforward and effective:
- Raw Material Loading: The raw materials required for concrete production are loaded into separate compartments of the volumetric mixer.
- Proportioning: Each ingredient is dispensed in pre-calibrated proportions, ensuring exact ratios for a specific mix design.
- Mixing: Once the materials are loaded and proportioned, the mixer combines them to create a homogeneous concrete mix.
- Delivery: The mixed concrete is then pumped directly from the volumetric plant to the location required on the construction site, eliminating the need for transportation.
Benefits of Using a Volumetric Concrete Plant
Utilizing a volumetric concrete plant brings numerous advantages to construction projects:
1. On-Demand Production
One of the most significant advantages is the ability to produce concrete on demand. This flexibility allows construction teams to adjust the mix according to project requirements, ensuring they have the right amount of concrete when needed.
2. Reduced Waste
Traditional concrete mixing often results in excess material due to overproduction. Volumetric mixing minimizes waste by producing only what is necessary, thereby conserving resources and reducing costs.
3. Cost Efficiency
Because of the reduced waste and the ability to mix on-site, volumetric concrete plants can lead to significant cost savings. This efficiency allows builders to allocate their budgets to other essential aspects of the project.
4. Quality Control
With volumetric plants, consistency and quality of the concrete can be better controlled. The ability to fine-tune the mixture in real time ensures that the concrete meets specified standards and performance criteria.
5. Versatility
Volumetric concrete plants can cater to various types of projects, from small residential jobs to large commercial builds. Their adaptability makes them an invaluable tool for any contractor.
Applications of Volumetric Concrete Plants
The versatility of volumetric concrete plants allows for a wide range of applications in construction, including:
- Residential Construction: Ideal for pouring foundations, driveways, and patios.
- Commercial Projects: Suitable for large-scale projects requiring significant concrete volumes.
- Road Construction: Used for creating pavement and concrete roads due to their on-site mixing capability.
- Infrastructure: Essential for the rapid development of bridges, tunnels, and other infrastructure needs.
The Technology Behind Volumetric Concrete Plants
The technology integrated into volumetric concrete plants is a major factor in their efficiency and effectiveness. Key elements include:
1. Automated Systems
Modern volumetric concrete plants feature automated systems that facilitate the precise measurement and mixing of materials. These advancements reduce human error and enhance operational efficiency.
2. Computerized Controls
Computerized controls allow operators to monitor and adjust the mixing process on-the-fly. This technology helps ensure that the correct mix is achieved every time, which is critical for high-quality concrete production.
3. Load Cells for Measurement
Load cells help in accurately weighing materials as they are added to the mixer. This precision is crucial for producing concrete that meets exact specifications.
Choosing the Right Volumetric Concrete Plant
When selecting a volumetric concrete plant for your construction projects, consider the following factors:
- Capacity: Choose a plant that meets the volume requirements of your projects.
- Mobility: Determine whether the plant needs to be transported frequently to different job sites or if it will remain in a single location.
- Features: Look for advanced features such as automated controls and real-time monitoring options.
- Manufacturer Reputation: Opt for reliable manufacturers known for producing high-quality volumetric plants.
Comparison with Traditional Concrete Batch Plants
Understanding the differences between a volumetric concrete plant and traditional batch plants is crucial for contractors facing specific project requirements:
AspectVolumetric Concrete PlantTraditional Batch PlantProduction MethodOn-demand mixing and deliveryBatch mixing in large quantitiesWaste ManagementMinimal waste due to precise mixingPotential for excess concrete and wasteTransport EfficiencyMix on-site and deliverRequires transport of pre-mixed concreteVersatilityHighly adaptable to various project sizesUsually suited for large projectsThe Future of Volumetric Concrete Plants
The future looks promising for volumetric concrete plants as technology continues to advance. Innovations such as:
- Smart Technology: Integration of IoT devices for monitoring efficiency and performance.
- Sustainability Initiatives: Eco-friendly production methods and materials to minimize environmental impact.
- Increased Automation: Further automation of the mixing and delivery processes to enhance efficiency.
As construction demands continue to evolve, volumetric plants remain at the forefront of innovative solutions, helping businesses like Polygon Machinery solidify their position within the industry.
Conclusion
In conclusion, the volumetric concrete plant represents a significant advancement in concrete production technology, offering numerous benefits including waste reduction, cost efficiency, quality control, and versatility. As more construction firms adopt this technology, we can expect to see significant improvements in the way concrete is produced and utilized across various construction all sectors. The move toward streamlined, on-demand concrete mixing is not just a trend—it's the future of the industry.