The Art and Science of Vacuum Casting
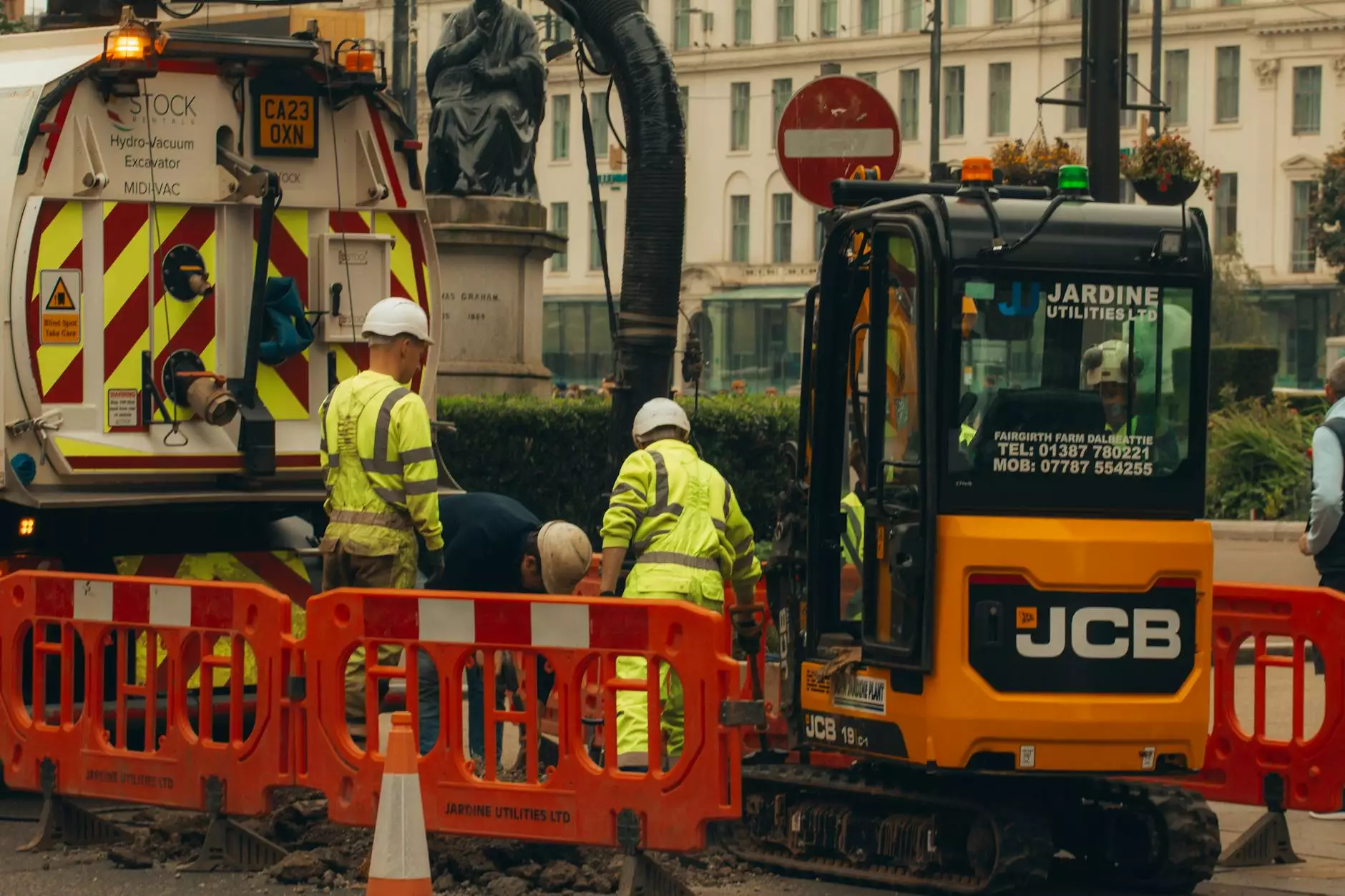
In the world of product design and 3D printing, the methodologies and technologies we choose can make a profound difference in the quality and efficiency of our outcomes. One of the most compelling techniques that have transcended industries—ranging from automotive to medical to consumer goods—is vacuum casting. This innovative process enables designers and manufacturers to create high-quality prototypes and components quickly while ensuring precision and fidelity to original designs.
What is Vacuum Casting?
Vacuum casting is a manufacturing process that involves creating a mold from a master pattern, typically made from materials such as polyurethane, silicone, or other elastomers. The key to vacuum casting lies in its use of a vacuum to draw the casting material into the mold, effectively eliminating air bubbles and ensuring a smooth, uniform finish. This method is particularly valuable when producing parts in low to medium volumes, making it an economical choice for startups and design firms alike.
How Does Vacuum Casting Work?
The vacuum casting process can be broken down into several critical steps:
- Master Pattern Creation: A master model is created using materials such as resin or 3D printing. This model serves as the basis for the mold.
- Mold Production: The master pattern is encased in silicone to create a flexible mold. This process captures every intricate detail of the original design.
- Vacuum Casting: The silicone mold is then placed in a vacuum chamber. Liquid casting material, usually polyurethane resin, is poured into the mold. The vacuum seals the mold and protects against air entrapment.
- Curing: The casting material is allowed to cure, solidifying into the desired shape.
- Demolding: After curing, the mold is carefully opened to release the cast part. This can be repeated multiple times to create several copies.
Benefits of Vacuum Casting
Vacuum casting offers a myriad of advantages, making it a preferred choice for businesses in the product design and 3D printing arenas. Here are some key benefits:
- High Detail and Precision: The use of a silicone mold allows for exceptionally high detail, capturing intricate features that more traditional methods may miss.
- Cost-Effective for Short Runs: For small production runs, vacuum casting can be significantly more cost-effective compared to traditional injection molding.
- Rapid Prototyping: The speeds associated with vacuum casting enable businesses to test concepts and designs rapidly, leading to quicker product development cycles.
- Diverse Material Options: Various materials can be used for casting, allowing companies to select the best fit for their specific applications, including various hardness levels and finishes.
- Versatility: Vacuum casting is suitable for various industries, including automotive, electronics, and consumer products, providing businesses with flexible manufacturing solutions.
Applications of Vacuum Casting in Product Design
Vacuum casting has numerous applications, particularly in product design. Here are some areas where this innovative technology shines:
1. Product Prototyping
Developing a prototype is integral to the product design process. Vacuum casting facilitates the rapid creation of prototypes that are not only accurate but also functional. Designers can iterate quickly, testing and refining their ideas before committing to more expensive manufacturing methods.
2. Functional Testing
With vacuum casting, companies can produce test parts that replicate the final product's material properties. This ensures that designs are not only viable but also ready for real-world use. Engineers can conduct stress tests, ergonomic evaluations, and more, providing valuable feedback for future iterations.
3. Low-Volume Production
For small businesses or startups, mass production may not be feasible. Vacuum casting allows for the production of low-volume runs of parts and products, enabling companies to launch new products without the burden of significant investment in machinery and tooling.
4. Customization and Limited Editions
Artists and designers often seek to create unique pieces or limited edition products. Vacuum casting allows for the customization of molds and products, enabling designers to offer clients bespoke options that stand out in a crowded market.
Vacuum Casting vs. Other Methods
When contemplating manufacturing options, it's essential to compare vacuum casting with other methods, such as injection molding or 3D printing. Here is a brief overview:
1. Vacuum Casting vs. Injection Molding
Injection molding is often favored for high-volume production due to its speed and efficiency. However, it requires significant upfront investment in molds and tooling, making it less accessible for startups. In contrast, vacuum casting allows for lower startup costs and greater flexibility in design iterations, making it ideal for product development stages.
2. Vacuum Casting vs. 3D Printing
While 3D printing excels in rapid prototyping and singular custom parts, it can often struggle with producing high-quality surface finishes in larger volumes. Vacuum casting, however, achieves superior surface finishes and higher consistency across multiple parts while maintaining the flexibility of design.
Choosing the Right Partner for Vacuum Casting
When considering vacuum casting for your next project, selecting a capable partner is crucial. Here are some tips for finding the right company to assist you:
- Experience and Specialization: Look for companies with a proven track record in vacuum casting specific to your industry.
- Material Options: Ensure that they offer a diverse range of materials that suit your needs and can replicate the desired attributes of your final product.
- Portfolio of Past Work: Examine their previous projects to gauge the quality and variety of their casting capabilities.
- Customer Testimonials: Reviews and testimonials from past clients can provide insights into the company’s reliability and service quality.
- Communication: A good partner will prioritize open communication to ensure that your vision translates into the final product effectively.
The Future of Vacuum Casting in Business
As technology evolves, vacuum casting continues to be at the forefront of innovation in product design and manufacturing. With advancements in materials, such as bio-based resins and improved silicone methodologies, the quality and application range of vacuum casting are set to expand significantly. This evolution allows companies to embrace sustainability while maintaining high standards of production.
Embracing Sustainability
Today’s consumers are increasingly aware of environmental issues. As a result, there is growing pressure on businesses to seek out sustainable production methods. Advances in vacuum casting technology are leading to the development of eco-friendly materials that reduce the environmental impact during manufacturing processes. By embracing these innovations, businesses can cater to eco-conscious consumers while also positioning themselves as leaders in sustainability efforts in their industries.
Conclusion
In summary, vacuum casting stands out as a transformative technique in the fields of product design and 3D printing. Its unmistakable benefits—from rapid prototyping and cost-efficiency to high-quality results—make it an invaluable asset for businesses looking to innovate and excel. As we look to the future, the commitment to adopting sustainable practices and exploring new materials will ensure that vacuum casting remains a vital part of the modern manufacturing landscape.
For businesses ready to enhance their product design capabilities, consider incorporating vacuum casting into your workflow. Partner with experienced professionals in the industry, and leverage this powerful method to bring your creative visions to life.