Understanding Injection Mold Tools: A Comprehensive Guide
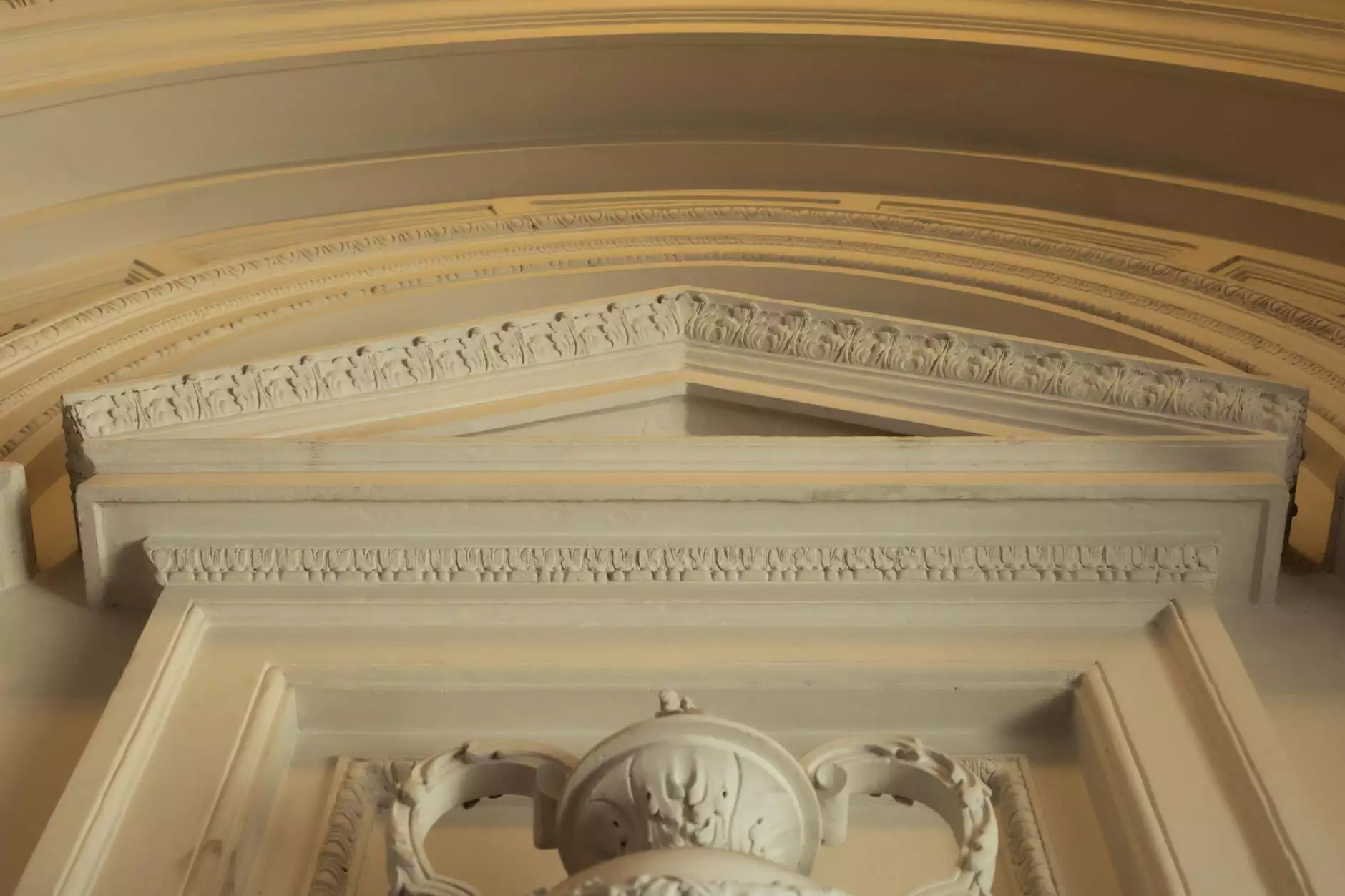
Injection mold tools play a crucial role in the manufacturing sector, especially for companies involved in mass production of plastic components. This guide will delve into the intricacies of injection mold tools, discussing their design, functionality, benefits, and the overall impact on the industry.
What are Injection Mold Tools?
Injection mold tools are specialized devices used to create parts by injecting molten material into a mold. These molds are typically made from durable materials to withstand the high pressures and temperatures associated with the injection molding process. The primary materials used for manufacturing these molds include:
- Steel: Offers high durability and is ideal for high-volume production.
- Aluminum: Lighter and more cost-effective for lower volume runs.
- Copper: Used for its excellent thermal conductivity, allowing faster cooling and cycle times.
Types of Injection Mold Tools
There are various types of injection mold tools available in the market, each designed for specific applications and processes. Here are some common types:
1. Cold Runner Molds
Cold runner molds have channels that remain solid at all times. The advantages of cold runners include:
- Lower initial costs due to less complex design.
- Enhanced control over the part cooling process.
- Ability to produce multiple parts simultaneously.
2. Hot Runner Molds
Hot runner molds maintain the molten plastic in a fluid state right up to the point of injection. Their benefits are:
- Reduced waste as there is no solidified plastic to recycle.
- Improved cycle times leading to higher productivity.
- Better quality of molded parts due to consistent temperature management.
3. Multi-Cavity Molds
Multi-cavity molds allow the production of several identical parts simultaneously, which maximizes efficiency. Key advantages include:
- Enhanced production speed.
- Cost efficiency for high-volume production.
- Uniformity in production quality.
The Role of Injection Mold Tools in Manufacturing
Injection molding is one of the most versatile and widely used manufacturing processes. Here’s how injection mold tools contribute to the industry:
Efficiency and Speed
The use of injection mold tools allows for rapid production of components. This is particularly important for industries that require large volumes of parts, such as automotive, consumer goods, and electronics. The efficiency of using such tools minimizes production costs and leads to quicker turnaround times.
Precision and Quality
Another significant benefit of injection molding is the ability to produce highly precise parts. The tooling used can be engineered to very tight tolerances, ensuring that the final products meet the required specifications. This precision is crucial in applications where safety and performance are paramount.
Designing Injection Mold Tools
The design of injection mold tools is a complex process that requires expertise. Several factors must be considered during the design phase:
Material Selection
Choosing the right materials for both the mold and the molten plastic is critical. The selection depends on factors such as:
- The properties of the final product.
- The anticipated production volume.
- Cost considerations.
Mold Layout
An effective mold layout ensures that the molten material flows correctly, minimizing defects and optimizing cycle times. Important considerations include:
- Gate design and placement.
- Cooling channel design for efficient cooling.
- Parting lines and ejection systems.
Simulation and Testing
Before finalizing the mold design, simulations and tests are crucial. This stage allows for:
- Identifying potential design flaws.
- Optimizing cooling and injection processes.
- Predicting the performance of the mold in real-world conditions.
Applications of Injection Mold Tools
The versatility of injection mold tools makes them applicable across various industries. Some prominent applications include:
Automotive Industry
In the automotive sector, injection molding produces numerous parts, including:
- Dashboards and interior fittings.
- Fuel tanks and housing components.
- Service parts and assemblies.
Consumer Goods
Injection molding is essential in creating everyday consumer products such as:
- Bottles and containers.
- Kitchenware and utensils.
- Toys and electronic housings.
Medical Devices
The medical industry leverages injection molding for producing high-quality, sterile components. Examples include:
- Medical device casings.
- Disposable syringes and surgical tools.
- Implants and diagnostic devices.
Advantages of Using Injection Mold Tools
Utilizing injection mold tools offers several advantages for manufacturers:
Cost-Effectiveness
Although the initial investment in mold creation can be significant, the long-term savings through reduced production costs make it worthwhile. The high-speed production capabilities help recover costs quickly.
Sustainability
Modern injection molding techniques emphasize recycling and sustainability. Excess material can often be reused, and advances in technology are leading to the creation of bioplastics, further enhancing sustainability efforts.
Versatility
Injection mold tools accommodate a wide range of materials beyond just plastics, enabling the creation of complex geometries and multi-material assemblies. This versatility allows manufacturers to innovate and create niche products that meet specific consumer needs.
Future Trends in Injection Molding
The world of injection molding is evolving with technology. Some emerging trends include:
Industry 4.0 and Automation
As manufacturing heads toward Industry 4.0, the integration of IoT (Internet of Things) in injection mold tools is becoming prevalent. This allows for:
- Real-time monitoring of the production process.
- Predictive maintenance to reduce downtime.
- Data analytics for improved decision-making.
3D Printing of Molds
The advent of 3D printing technology is revolutionizing mold making. Companies can now produce prototypes and molds faster, more economically, and with less waste, leading to:
- Reduction in product development time.
- Lower upfront costs for startups and smaller manufacturers.
Conclusion
Understanding injection mold tools is essential for any business looking to thrive in the manufacturing industry. From improved efficiency and quality to cost savings and sustainability, these tools are indispensable. As technology continues to advance, the potential for innovation in injection molding is limitless, paving the way for smarter manufacturing solutions. Embrace the power of injection mold tools and position your business for success in a competitive landscape.